Our Handcrafted Process
It's all in the details.
Since Buckle first began to produce braces in the 1940's and belts in the 1960's, our finely handcrafted accessories have remained our signature products, renowned for timeless style and Australian made quality.
We craft leather belts and braces using traditional processes and hand-assisted machinery in our Sydney facility.
Each handcrafted piece tells a story, honouring the skills and traditions passed down by our talented craftspeople.
We invite you to discover the processes behind our Australian made accessories.
Take a look behind the scenes in our production facility in Stanmore, NSW, where we locally handcraft our belts and braces.
Crafting Australian Made Belts
Since the 1940’s, we have locally handcrafted leather belts using traditional techniques and hand-assisted machinery.
With each handcrafted belt, we honour the traditions passed down by our skilled craftspeople, ensuring that every piece tells a story of timeless style and fine Australian craftsmanship.
We begin by carefully cutting and preparing the leather hides, squaring them up for further processing. Next, the leather pieces are fed through a specialized cutting machine, creating long, thin strips for the belt foundation.
The top leather is then joined with a backing using glue and combining machines, followed by the punching of arrow-shaped tips for the buckle. We trim the belt during the gluing process to remove any untidy edges, ensuring a clean finish.
Elongated holes called slots are punched at the buckle end, while prong holes are punched at the tip end using various knives.
Skiving involves shaving off layers of leather at the buckle end, enabling easier folding. The straps undergo a light sanding process to remove rough edges before applying color to the edges, slots, and prong holes.
The belts are dried using a modern drying channel and then go through a gentle cleaning process, removing any excess color.
Some belts may undergo stitching along the edge for durability and aesthetics. Keepers, small leather loops, are crafted to tuck the tip end neatly.
Buckles are carefully placed onto the straps, and swing tickets are attached for information. Bartacking secures the buckle and keeper, followed by trimming excess thread.
Stamping is done with heated machines to imprint logos, size, country of origin, and identifiers onto the belts.
Finishing touches like hangers or barcodes are added to prepare the belts for display and protection during transit.
A final clean ensures the belts are in pristine condition, removing markings and traces.
Belts are then packed and undergo a thorough quality control inspection. Invoicing and dispatching complete the process, ensuring timely delivery to customers.
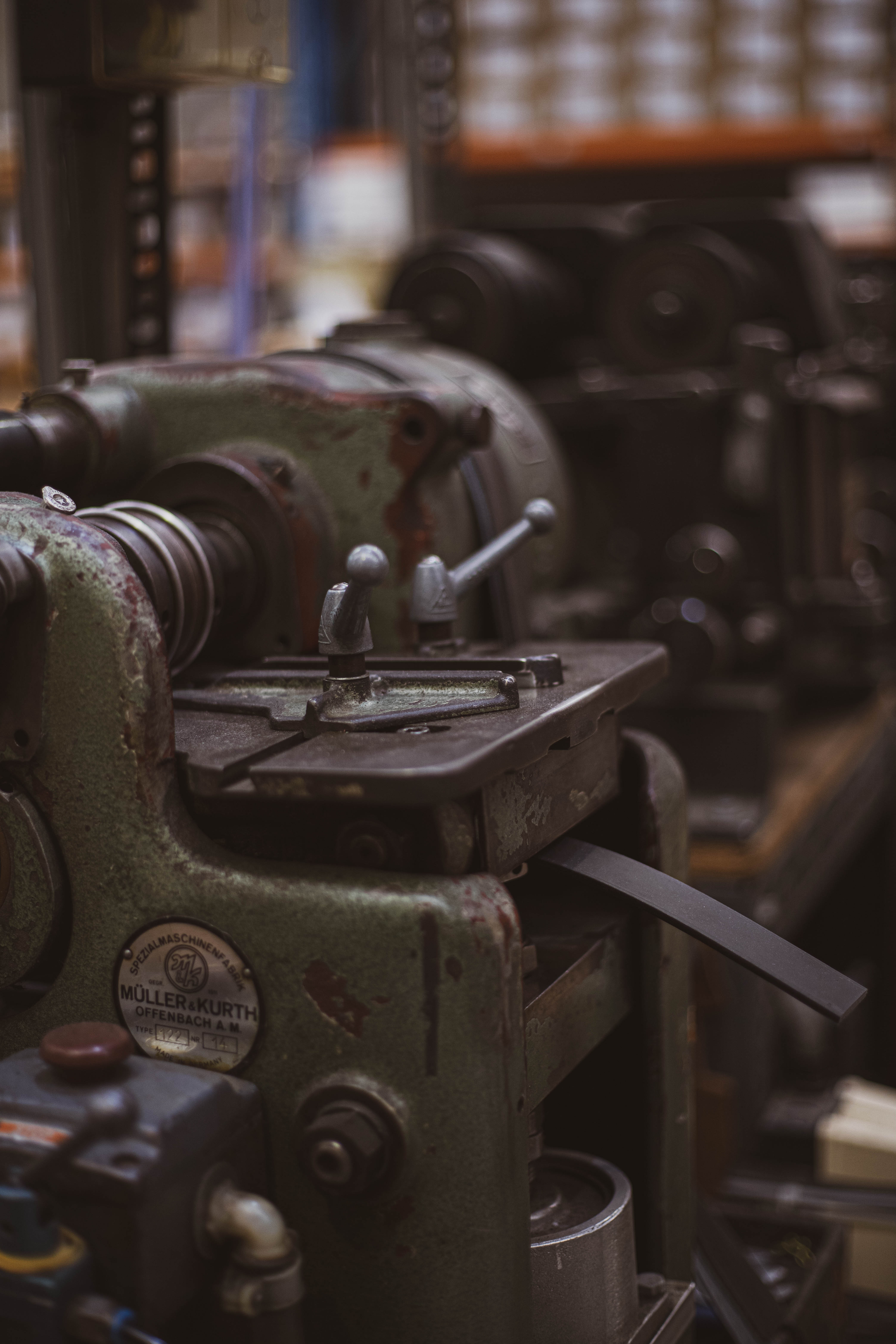
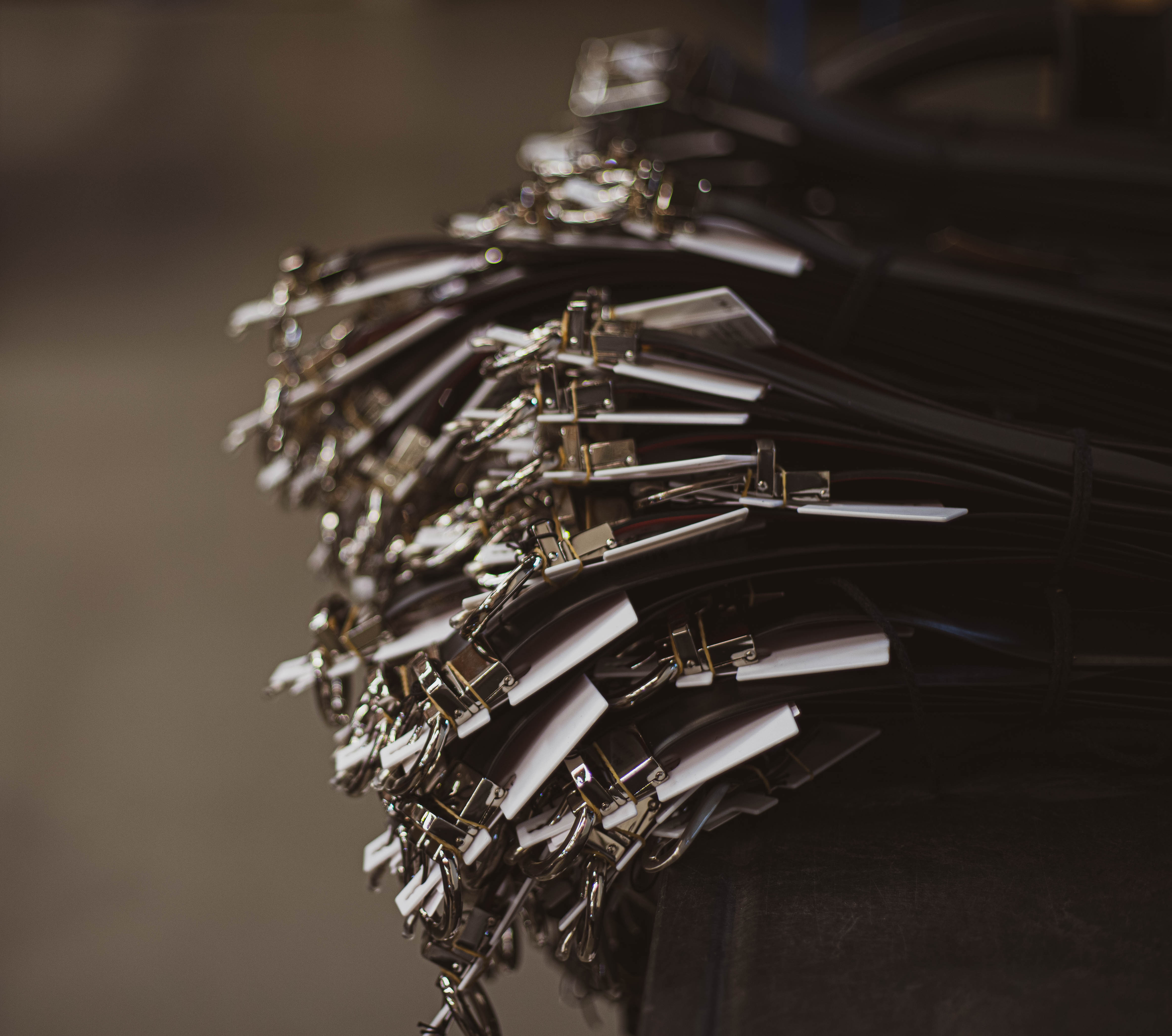
A final clean ensures the belts are in pristine condition.
Crafting Australian Made Braces
Since the 1920s, Buckle has been handcrafting braces in Sydney.
To this day, our handcrafted braces remain one of our best selling products. Our range features a variety of timeless and captivating patterns, including collaborations with esteemed Australian designers Jocelyn Proust and Ali Wilkinson.
We begin by sourcing high-quality elastic rolls from Belgium and carefully assessing their yield.
For smaller orders, our skilled craftspeople hand-cut the elastic using scissors and cutting tables, while larger orders are cut using a specialized press.
We punch out tabs from scrap leather to use in our braces, either as triangles for Y-back braces or longer pieces for leather tab ends.
Y-back braces are created by joining elastic lengths with leather triangles using a sewing machine, while X-back braces utilize butterfly clips.
Metal adjusters are threaded onto the elastic to allow for resizing. The ends of the braces are sewn, offering options of pressed metal clips or traditional leather button ends.
The braces are packed, wrapped, and prepared for display with barcodes and relevant information.
During picking and packing, the braces are carefully consolidated, wrapped, and undergo a thorough quality control check.
Finally, our invoicing clerk ensures accurate weighing, invoicing, and booking of the order for delivery, completing the seamless production-to-customer delivery process.
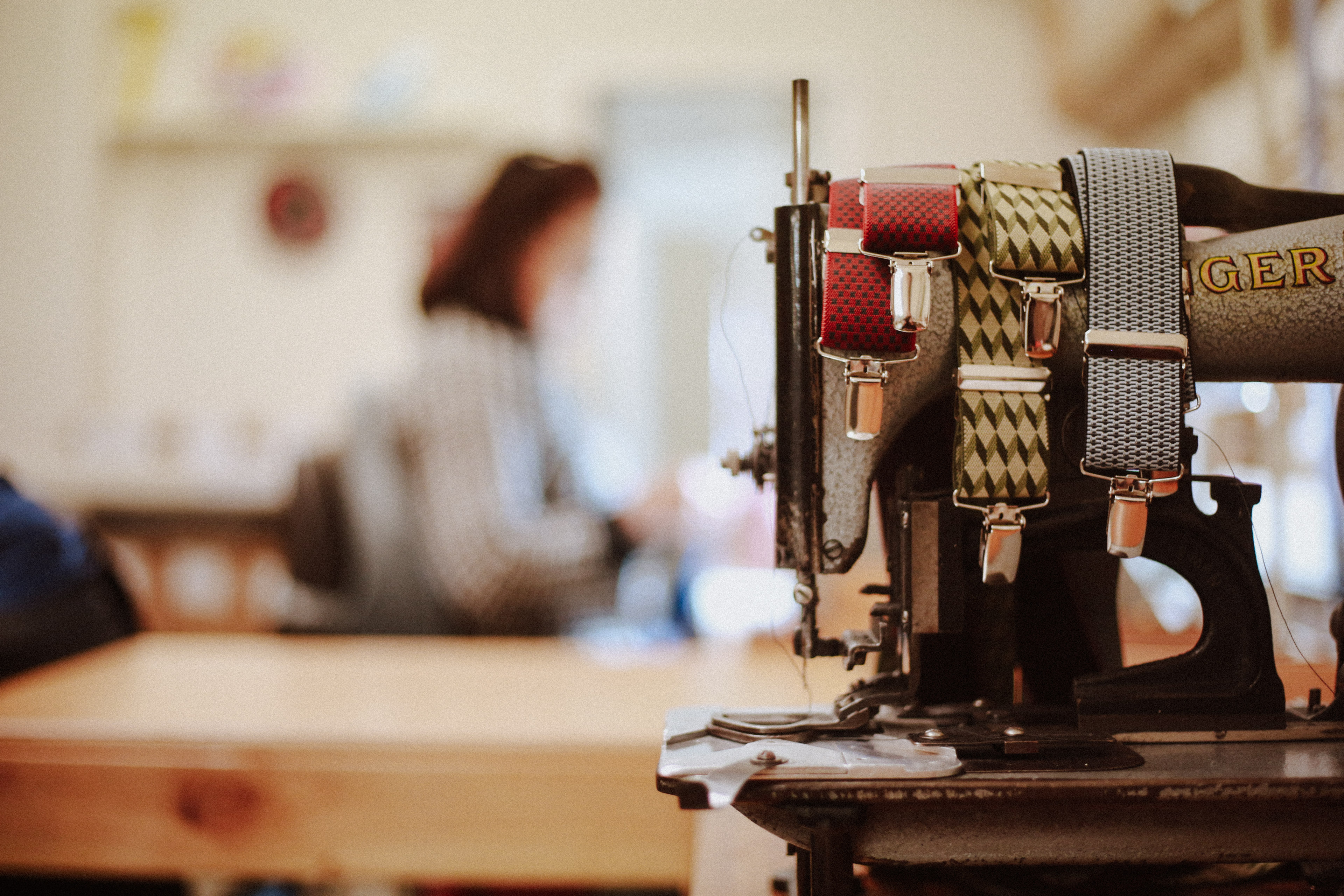
It was in 1960 when Buckle began its relationship with a Belgian elastic maker, and started to produce braces in a range of stripes and colours.
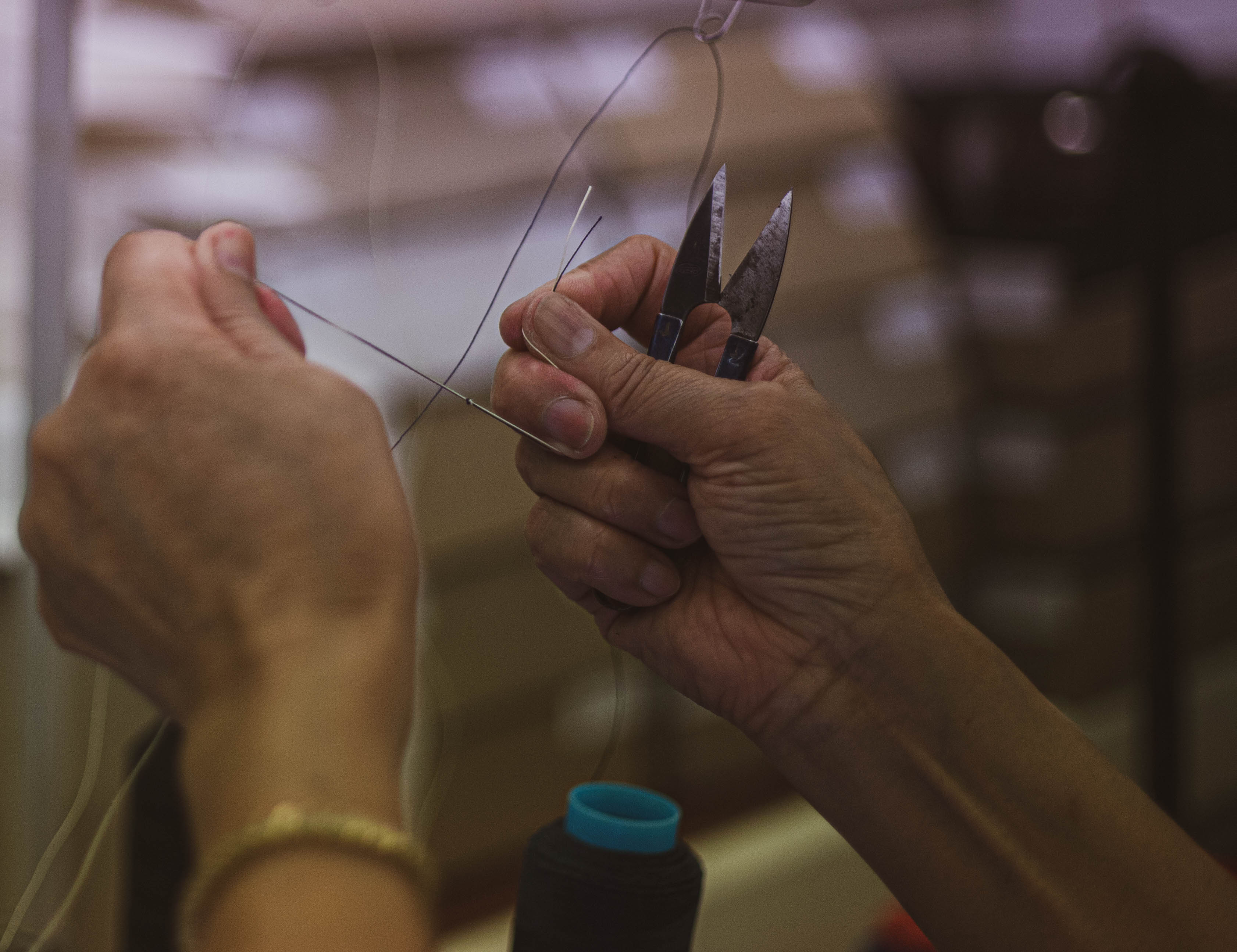
Learn more about us